Pilihan perawatan permukaan adalah masalah yang dihadapi setiap perancang. Ada banyak jenis pilihan perawatan permukaan yang tersedia, dan perancang tingkat tinggi tidak hanya mempertimbangkan ekonomi dan kepraktisan desain, tetapi juga memperhatikan proses perakitan dan bahkan persyaratan lingkungan. Di bawah ini adalah pengantar singkat untuk beberapa pelapis yang umum digunakan untuk pengencang berdasarkan prinsip -prinsip di atas, untuk referensi oleh praktisi pengikat.
1. Elektrogalvanisasi
Seng adalah lapisan yang paling umum digunakan untuk pengencang komersial. Harganya relatif murah, dan penampilannya bagus. Warna umum termasuk hijau hitam dan militer. Namun, kinerja anti-korosi rata-rata, dan kinerja anti-korosi adalah yang terendah di antara lapisan pelapisan seng (lapisan). Secara umum, uji semprotan garam netral dari baja galvanis dilakukan dalam waktu 72 jam, dan agen penyegelan khusus juga digunakan untuk memastikan bahwa uji semprotan garam netral berlangsung selama lebih dari 200 jam. Namun, harganya mahal, yaitu 5-8 kali lipat dari baja galvanis biasa.
Proses elektrogalvanisasi rentan terhadap embrittlement hidrogen, sehingga baut di atas kelas 10.9 umumnya tidak diobati dengan galvanisasi. Meskipun hidrogen dapat dihilangkan menggunakan oven setelah pelapisan, film pasif akan rusak pada suhu di atas 60 ℃, sehingga penghilangan hidrogen harus dilakukan setelah elektroplating dan sebelum pasif. Ini memiliki biaya operabilitas yang buruk dan biaya pemrosesan yang tinggi. Pada kenyataannya, pabrik produksi umum tidak secara aktif menghilangkan hidrogen kecuali diamanatkan oleh pelanggan tertentu.
Konsistensi antara torsi dan kekuatan pengetatan pra pengencang galvanis buruk dan tidak stabil, dan mereka umumnya tidak digunakan untuk menghubungkan bagian -bagian penting. Untuk meningkatkan konsistensi preload torsi, metode pelapisan zat pelumas setelah pelapisan juga dapat digunakan untuk meningkatkan dan meningkatkan konsistensi preload torsi.
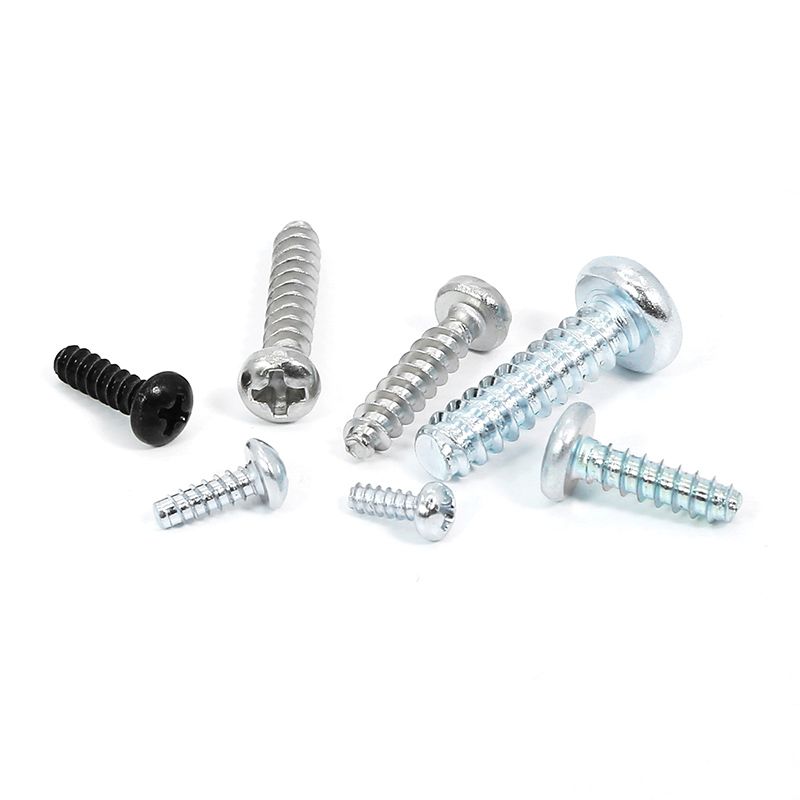
2. Fosfat
Prinsip dasar adalah bahwa fosfat relatif lebih murah daripada galvanisasi, tetapi resistensi korosionnya lebih buruk daripada galvanisasi. Setelah fosfasi, minyak harus diterapkan, dan ketahanan korosiasinya terkait erat dengan kinerja minyak yang diterapkan. Misalnya, setelah fosfat, mengoleskan minyak anti karat umum dan melakukan uji semprotan garam netral hanya 10-20 jam. Menerapkan minyak anti karat bermutu tinggi dapat memakan waktu hingga 72-96 jam. Tetapi harganya 2-3 kali lipat dari minyak fosfasi umum.
Ada dua jenis fosfat yang umum digunakan untuk pengencang, fosfat berbasis seng, dan fosfat berbasis mangan. Fosfasi berbasis seng memiliki kinerja pelumasan yang lebih baik daripada fosfat berbasis mangan, dan fosfasi berbasis mangan memiliki resistensi korosi yang lebih baik dan ketahanan aus daripada pelapisan seng. Ini dapat digunakan pada suhu mulai dari 225 hingga 400 derajat Fahrenheit (107-204 ℃). Terutama untuk koneksi beberapa komponen penting. Seperti baut batang penghubung dan mur mesin, kepala silinder, bantalan utama, baut roda gila, baut roda dan mur, dll.
Baut kekuatan tinggi menggunakan fosfat, yang juga dapat menghindari masalah embrittlement hidrogen. Oleh karena itu, baut di atas kelas 10.9 di bidang industri umumnya menggunakan perlakuan permukaan fosfasi.
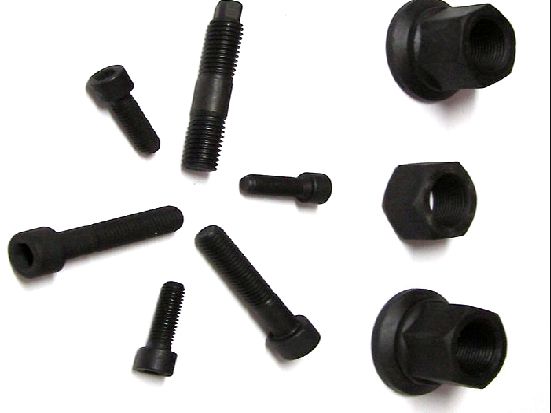
3. Oksidasi (menghitam)
Blackening+Oiling adalah lapisan populer untuk pengencang industri karena merupakan yang termurah dan terlihat bagus sebelum konsumsi bahan bakar. Karena menghitamnya, hampir tidak memiliki kemampuan pencegahan karat, sehingga akan berkarat dengan cepat tanpa minyak. Bahkan di hadapan minyak, uji semprotan garam hanya dapat bertahan selama 3-5 jam.
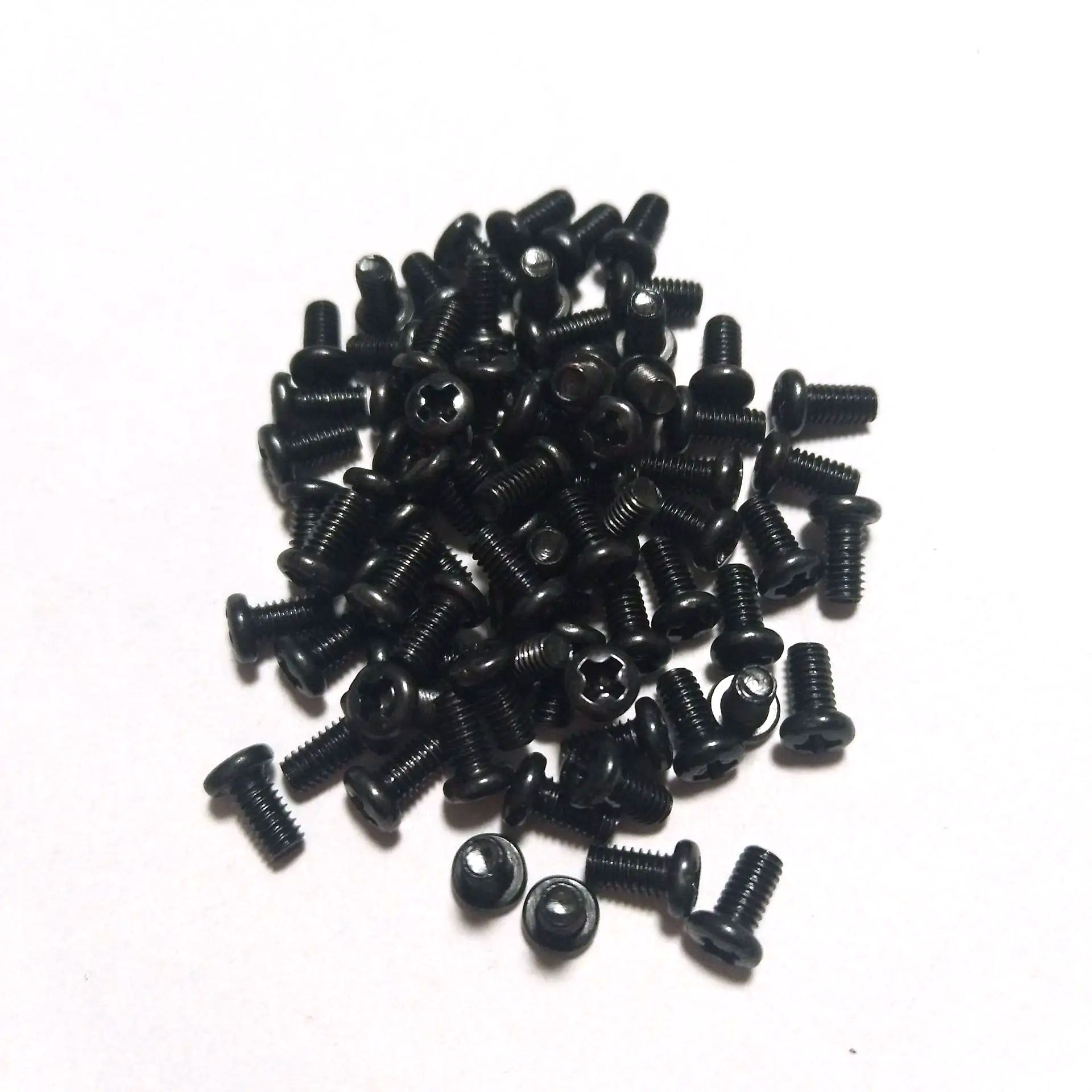
4. Partisi Elektroplating
Pelapisan kadmium memiliki ketahanan korosi yang sangat baik, terutama di lingkungan atmosfer laut, dibandingkan dengan perawatan permukaan lainnya. Biaya pengolahan cairan limbah dalam proses elektroplating kadmium tinggi, dan harganya sekitar 15-20 kali lipat dari seng elektroplating. Jadi itu tidak digunakan dalam industri umum, hanya untuk lingkungan tertentu. Pengencang yang digunakan untuk platform pengeboran minyak dan pesawat HNA.
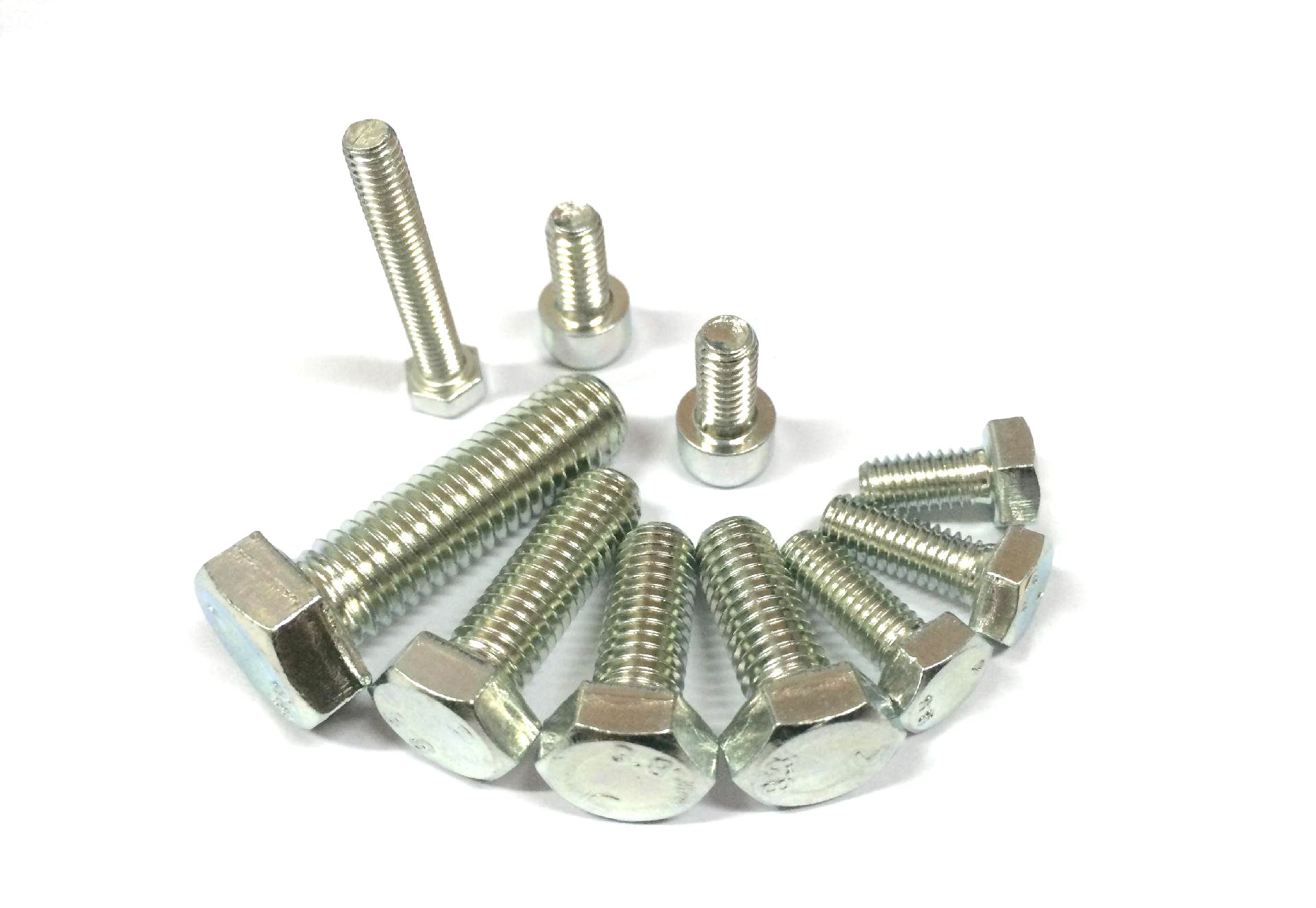
5. Pelapisan kromium
Lapisan kromium sangat stabil di atmosfer, tidak mudah untuk mengubah warna dan kehilangan kilau, dan memiliki kekerasan tinggi dan ketahanan aus yang baik. Penggunaan pelapisan kromium pada pengencang umumnya digunakan untuk tujuan dekoratif. Ini jarang digunakan di bidang industri dengan persyaratan resistensi korosi yang tinggi, karena pengencang berlapis krom yang baik sama -sama mahal seperti stainless steel. Hanya ketika kekuatan stainless steel tidak mencukupi, pengencang berlapis krom digunakan sebagai gantinya.
Untuk mencegah korosi, tembaga dan nikel harus dilapisi terlebih dahulu sebelum pelapisan krom. Lapisan kromium dapat menahan suhu tinggi 1.200 derajat Fahrenheit (650 ℃). Tetapi ada juga masalah embrittlement hidrogen, mirip dengan electrogalvanizing.
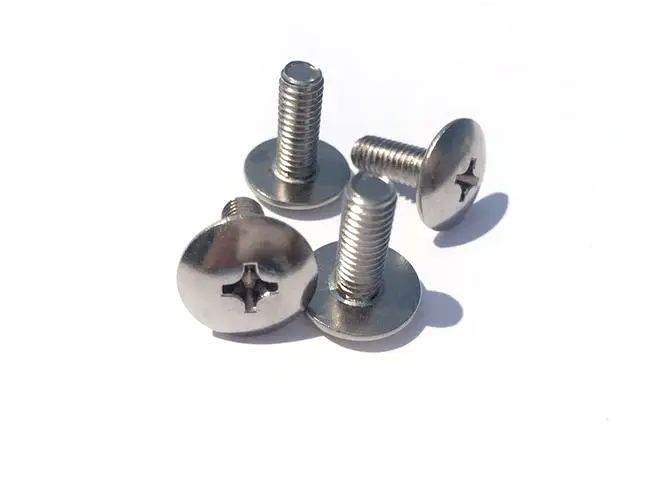
6. Pelapisan Nikel
Terutama digunakan di daerah yang membutuhkan anti-korosi dan konduktivitas yang baik. Misalnya, terminal baterai kendaraan yang keluar.
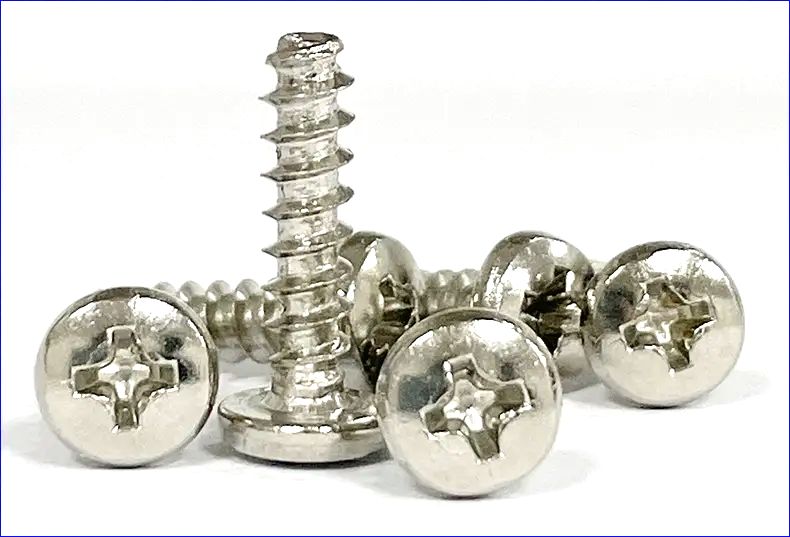
7. Hot-dip galvanizing
Galvanizing hot dip adalah lapisan difusi termal seng yang dipanaskan menjadi cairan. Ketebalan lapisan adalah antara 15 dan 100 μ m. Dan tidak mudah dikendalikan, tetapi memiliki ketahanan korosi yang baik dan sering digunakan dalam rekayasa. Selama proses galvanisasi hot dip, ada polusi yang parah, termasuk limbah seng dan uap seng.
Karena lapisan tebal, ia telah menyebabkan kesulitan dalam mengacaukan benang internal dan eksternal di pengencang. Karena suhu pemrosesan galvanisasi hot-dip, tidak dapat digunakan untuk pengencang di atas kelas 10.9 (340 ~ 500 ℃).
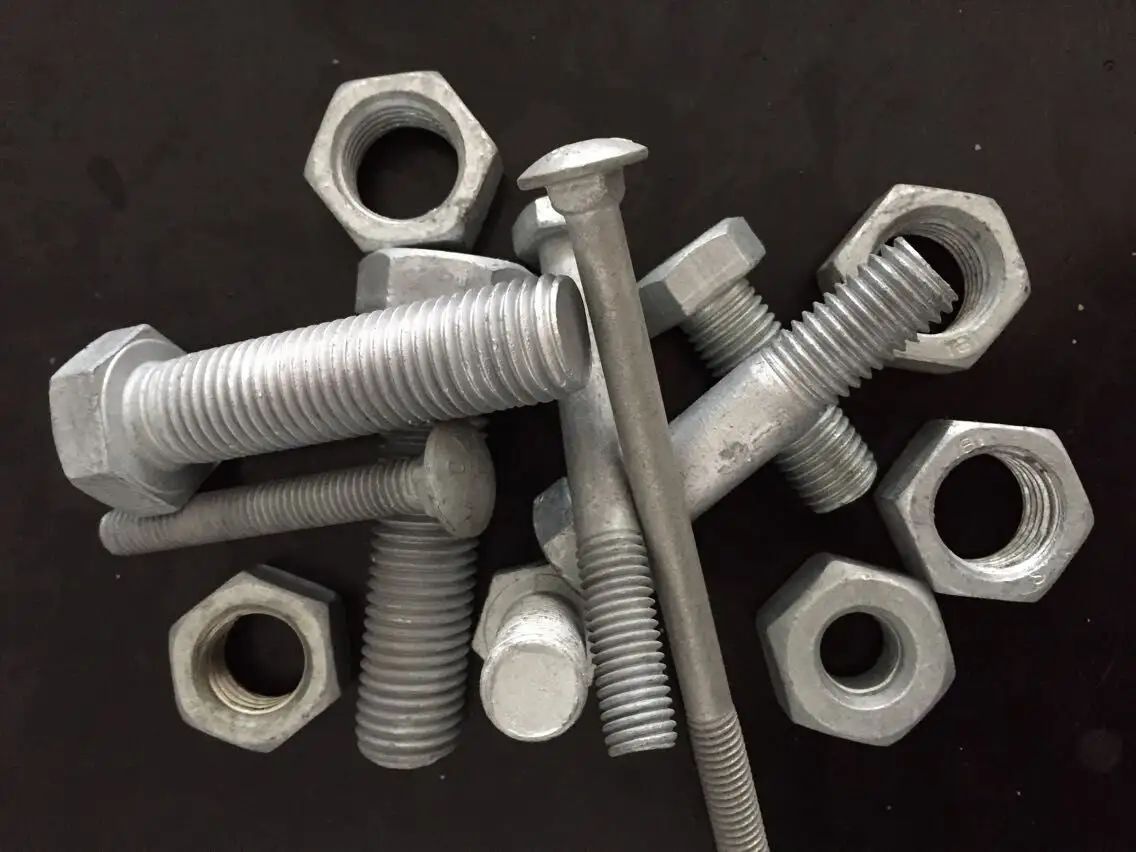
8. Infiltrasi seng
Infiltrasi seng adalah lapisan difusi termal metalurgi padat dari bubuk seng. Keseragamannya bagus, dan lapisan yang seragam dapat diperoleh di kedua benang dan lubang buta. Ketebalan pelapisan adalah 10-110 μ m. Dan kesalahan dapat dikontrol pada 10%. Kekuatan ikatannya dan kinerja anti-korosi dengan substrat adalah yang terbaik dalam pelapis seng (seperti elektrogalvanisasi, galvanisasi hot-dip, dan dacromet). Proses pemrosesannya bebas polusi dan paling ramah lingkungan.
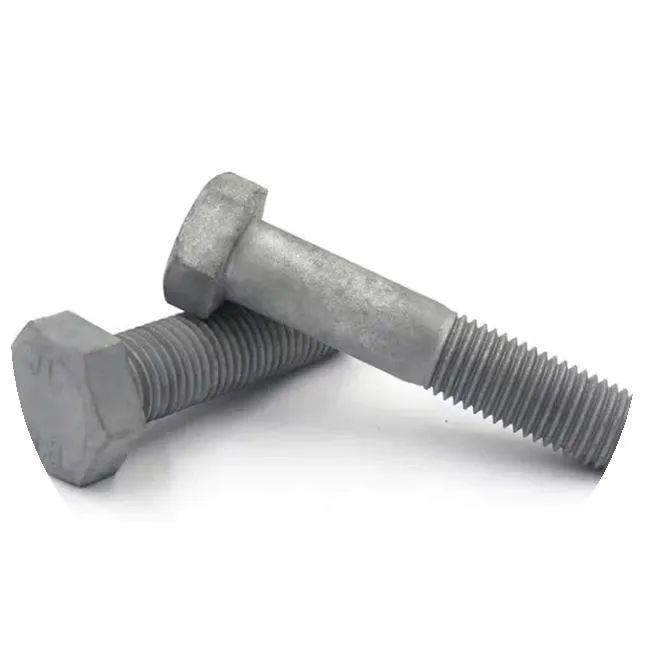
9. Dacromet
Tidak ada masalah embrittlement hidrogen, dan kinerja konsistensi preload torsi sangat baik. Tanpa mempertimbangkan masalah kromium dan lingkungan, Dacromet sebenarnya yang paling cocok untuk pengencang kekuatan tinggi dengan persyaratan anti-korosi yang tinggi.
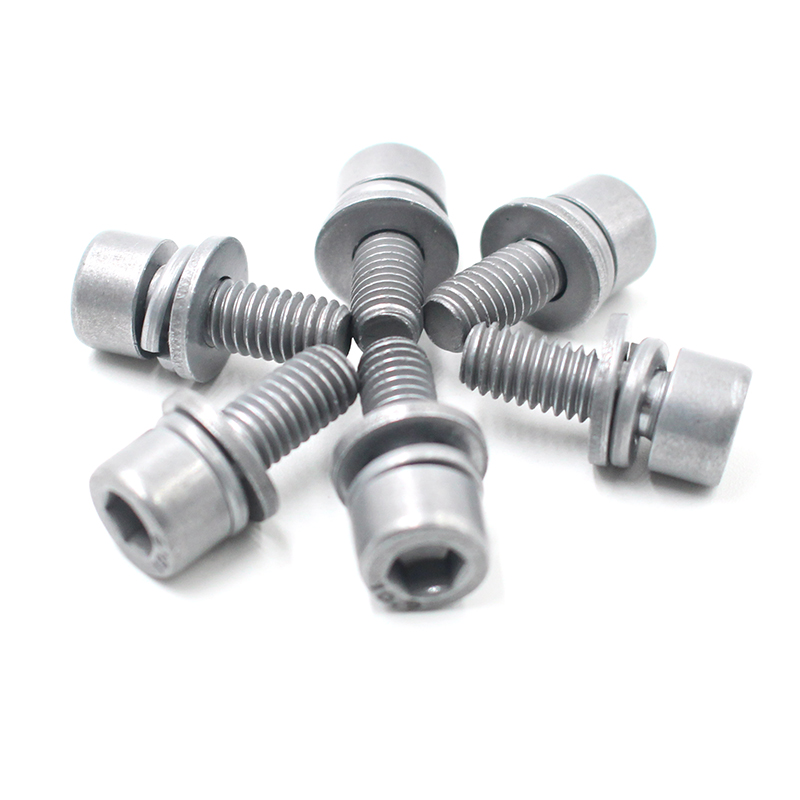
Waktu pos: Mei-19-2023